Трубчатые печи, как высокотемпературное экспериментальное оборудование, широко используются в таких областях, как материаловедение, химическая инженерия, металлургия и др. Они играют важную роль в различных высокотемпературных экспериментах и обработке материалов благодаря своей способности обеспечивать точный контроль температуры, регулируемые атмосферные условия и гибкую эксплуатацию.
Введение в трубчатые печи
Трубчатые печи, разработанные для обеспечения стабильных и эффективных высокотемпературных сред, широко используются в термической обработке материалов, контроле атмосферы и реакциях синтеза. Их уникальная структурная конструкция и система контроля температуры обеспечивают высокую гибкость и адаптивность в экспериментах, требующих точного нагрева и различных атмосферных условий.
- Принцип работы и конструктивные особенности трубчатых печей
Основные компоненты трубчатой печи включают нагревательную трубку, нагревательные элементы, систему контроля температуры и устройства контроля атмосферы. Нагревательная трубка обычно изготавливается из материалов, устойчивых к высоким температурам, таких как кварцевые или алюмосиликатные керамические трубки, которые могут выдерживать чрезвычайно высокие температуры. Нагревательные элементы обычно представляют собой резистивные провода или ленточные электронагреватели с хорошей проводимостью и высокой термостойкостью. Во время реакции нагревательный элемент передает энергию образцу внутри нагревательной трубки посредством электрического тока. Система контроля температуры контролирует температуру печи с помощью точных датчиков температуры и регулирует ее с помощью регулятора температуры для обеспечения стабильности при желаемой температуре реакции.
Конструкция трубчатой печи позволяет помещать образец внутрь трубчатого канала во время нагрева, при этом реагенты поступают и выходят через оба конца трубки. Система управления атмосферой регулирует приток и отток газов для поддержания требуемых атмосферных условий во время экспериментов, таких как инертные газы (азот, гелий), восстановительные газы (водород) и окислительные атмосферы.
- Применение трубчатых печей в высокотемпературном нагреве
Трубчатые печи широко используются в экспериментах, требующих точного высокотемпературного нагрева, таких как спекание, плавление и отжиг при обработке материалов. Высокотемпературный нагрев необходим, особенно при синтезе металлов, керамики и полупроводников. Эффективная функция нагрева трубчатой печи обеспечивает равномерный нагрев образцов, гарантируя полноту и последовательность реакций.
Например, во время спекания керамических материалов трубчатая печь нагревает керамический порошок при высоких температурах, способствуя связыванию частиц для образования твердого материала с определенной механической прочностью. Этот процесс обычно требует точного контроля температуры и атмосферы, чтобы избежать реакций окисления или восстановления, которые могут повлиять на конечное качество.
- Применение трубчатых печей для контроля атмосферы
Другим существенным преимуществом трубчатых печей является их способность проводить эксперименты в различных атмосферных условиях. Регулируя расход, тип и давление газов, трубчатые печи могут обеспечить необходимую среду для различных химических реакций. Конкретные области применения включают:
- Реакции окисления: Используется для окисления металлов. Например, окисление железа может быть проведено в высокотемпературной кислородной атмосфере для содействия образованию оксида железа (Fe₂O₃).
- Реакции восстановления: Достигается с помощью инертных или восстановительных газов (например, водорода) для восстановления оксидов металлов. Например, оксид меди может быть восстановлен до металлической меди в атмосфере водорода.
- Эксперименты в инертной атмосфере: Например, эксперименты по порошковой металлургии, проводимые в атмосфере азота или гелия, могут предотвратить реакцию образца с кислородом при высоких температурах, гарантируя чистоту реакционных материалов.
- Применение трубчатых печей в синтезе материалов
Трубчатые печи играют решающую роль в химическом синтезе, подготовке материалов и каталитических исследованиях. В частности, в областях высокотемпературного синтеза и осаждения из паровой фазы трубчатые печи обеспечивают идеальную среду для контроля температуры и реакционных атмосфер. Например, реакции химического осаждения из паровой фазы (CVD) с использованием трубчатой печи могут синтезировать тонкопленочные материалы. Во время этого процесса реагирующие газы нагреваются до определенной температуры внутри трубчатой печи, а газовые реакции образуют твердые пленки, которые осаждаются на поверхности подложки.
Кроме того, трубчатые печи могут использоваться для подготовки и модификации катализаторов. Активность катализатора часто тесно связана с его поверхностной структурой и фазой, и трубчатые печи могут использоваться для обработки катализаторов в различных атмосферах и температурах для корректировки их поверхностных свойств и повышения каталитических характеристик.
- Применение трубчатых печей при термической обработке металлов
Термическая обработка металла является еще одной важной областью применения трубчатых печей, особенно в таких процессах, как отжиг, закалка и упрочнение металлов, таких как сталь и алюминиевые сплавы. Процесс отжига включает в себя нагрев металла до определенной температуры и поддержание ее в течение определенного периода перед медленным охлаждением с целью снятия напряжения и улучшения пластичности и вязкости. Закалка включает в себя быстрое охлаждение металла для повышения твердости и прочности.
Трубчатые печи обеспечивают идеальные условия для термообработки благодаря точному контролю температуры и атмосферы, гарантируя, что металлические материалы приобретут желаемые механические свойства и микроструктуру.
- Перспективные тенденции развития трубчатых печей
С постоянным технологическим прогрессом применение трубчатых печей в высокотемпературных экспериментах и обработке материалов станет еще более распространенным. Будущие разработки могут быть сосредоточены на следующих областях:
- Точный контроль температуры: Благодаря более совершенной технологии контроля температуры трубчатые печи будут обеспечивать еще более стабильную и точную температурную среду для удовлетворения более сложных экспериментальных требований.
- Диверсификация управления атмосферой: Будущие трубчатые печи могут интегрировать больше типов систем управления газом для удовлетворения потребностей более широкого спектра реакций.
- Интеллектуальная Автоматизация: Системы автоматического управления трубчатыми печами будут и дальше совершенствоваться для повышения простоты эксплуатации и безопасности.
Заключение
Трубчатые печи играют незаменимую роль как критическое оборудование в высокотемпературных экспериментах во многих научных исследованиях и промышленных приложениях. Их применение в высокотемпературном нагреве, контроле атмосферы, синтезе материалов и термической обработке металлов достигло значительного успеха. С постоянным технологическим прогрессом сфера применения трубчатых печей будет продолжать расширяться, играя все более важную роль в таких областях, как материаловедение и химическая инженерия.
Трубчатая печь Kemi TFV-1200-50-I-220
Кеми TFV-1200-50-I-220 это компактный, вертикальная трубчатая печь открытого типа предназначена для спекания, закалки и экспериментов по химическому осаждению из газовой фазы в вакууме или атмосферных условиях. С диаметром трубки φ30/50 мм, она оснащена камерой из высокочистого оксида алюминия, нагревательными элементами, легированными молибденом, и максимальной температурой 1200 °C (номинальная температура 1100 °C). Печь включает в себя систему автоматического регулирования температуры PID с 30 программируемыми сегментами для точного управления (±1 °C). Она также поддерживает приложения с псевдоожиженным слоем для осаждения поверхности порошка, используя сердечник из кварцевого песка для подвешивания частиц образца в зоне нагрева. Печь разработана для легкой замены трубки и имеет номинальную мощность 1,5 кВт.
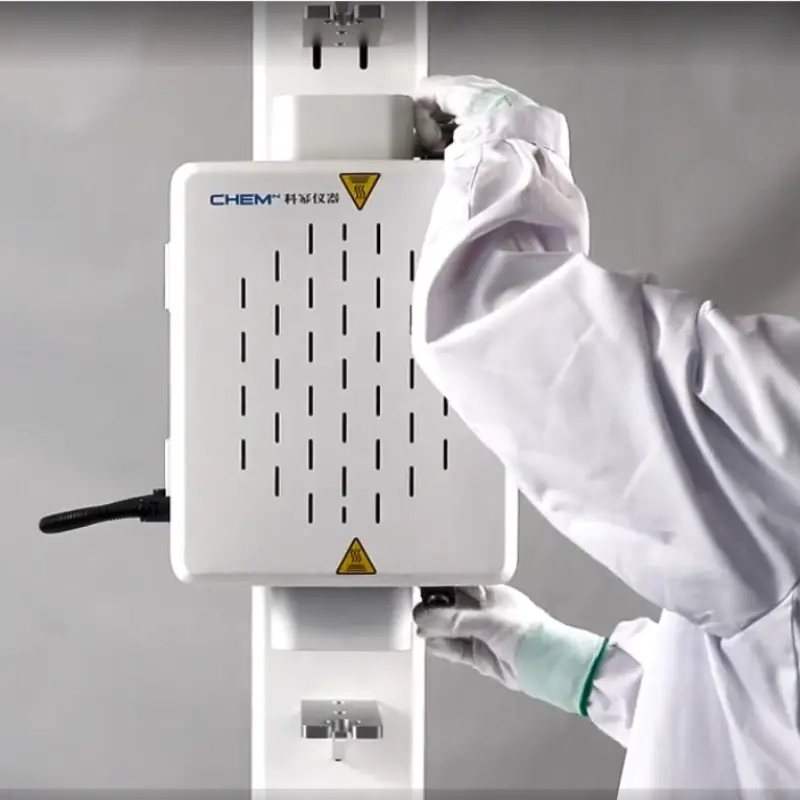
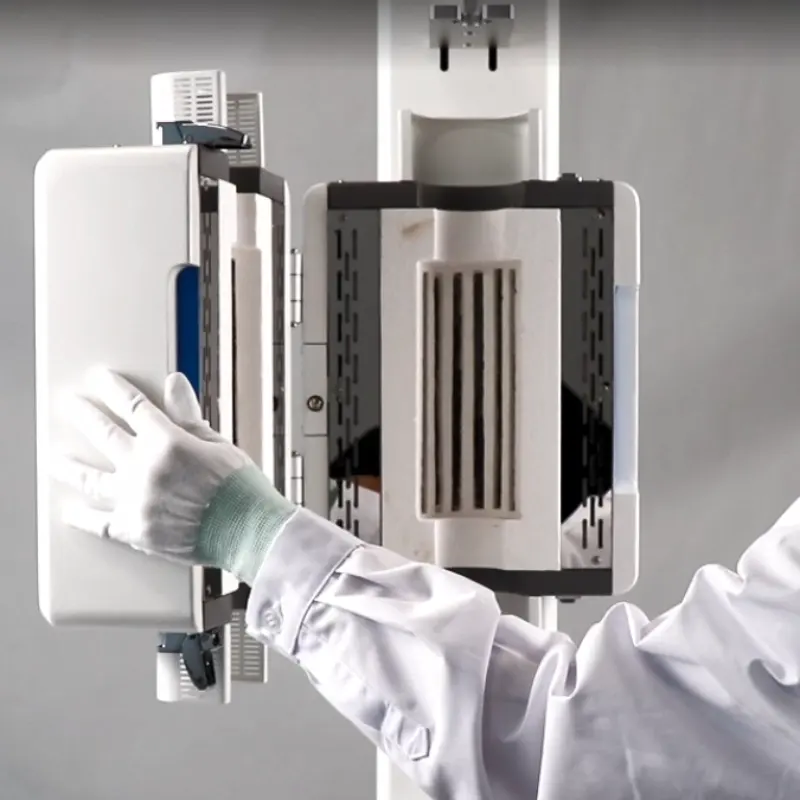
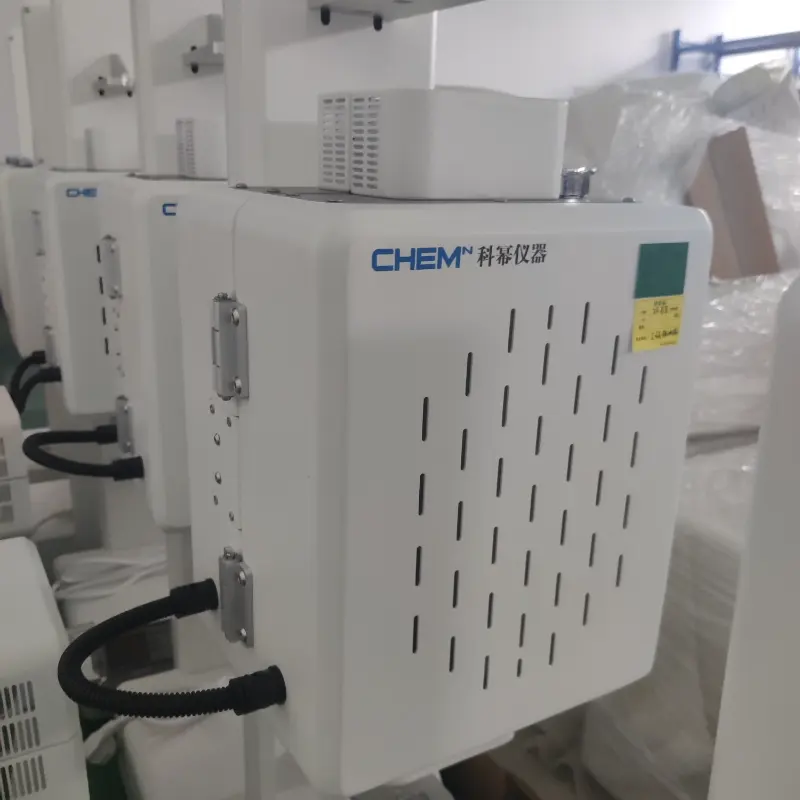