Der Muffelofen als Hochtemperatur-Experimentiergerät wird häufig in Bereichen wie Materialwissenschaft, Chemieingenieurwesen und Metallschmelze eingesetzt. Seine Hauptfunktion besteht darin, eine sauerstofffreie oder sauerstoffarme Umgebung mit hoher Temperatur für die Wärmebehandlung von Proben, das Sintern, die Veraschung und andere Experimente bereitzustellen. Diese Arbeit untersucht detailliert das Funktionsprinzip, die wichtigsten Anwendungen und den Einsatz in verschiedenen Bereichen, darunter Metallwärmebehandlung, Keramiksintern und chemische Analyse. Durch die detaillierte Analyse der Reaktionsprozesse werden die Bedeutung und die Vorteile des Muffelofens in Hochtemperaturexperimenten hervorgehoben.
1. Einführung in den Muffelofen
Muffelofen Hochtemperatur-Versuchsgerät Kennzeichnet sich durch seine abgedichtete Heizkammer aus, die den direkten Kontakt der Probe mit Sauerstoff oder anderen Gasen verhindert. Diese Konstruktion ermöglicht es dem Ofen, die notwendige Wärmebehandlungsumgebung für Versuchsproben bei präzise kontrollierten Temperaturen bereitzustellen. Mit der Weiterentwicklung der Technologie findet der Muffelofen breite Anwendung in verschiedenen Forschungsbereichen wie der Materialverarbeitung, der Umweltüberwachung, der Arzneimittelprüfung und der Metallverhüttung. Diese Arbeit erläutert das Funktionsprinzip und die wichtigsten Anwendungen des Muffelofens aus der Perspektive von Reaktionsprozessen.
2. Funktionsprinzip des Muffelofens
Die Grundstruktur eines Muffelofens besteht aus Ofenkörper, Heizelementen, Temperaturregelsystem und Ofentür. Der Ofenkörper besteht üblicherweise aus hochtemperaturbeständigen Materialien (wie feuerfesten Steinen oder Keramik), die die äußere Wärme effektiv isolieren. Die Heizelemente im Ofen (wie Widerstandsdrähte) sind gleichmäßig verteilt und sorgen für Hochtemperaturumgebungen von Raumtemperatur bis über 1700 °C. Das mit Präzisionstemperatursensoren und Regelgeräten ausgestattete Temperaturregelsystem gewährleistet eine stabile und genaue Temperaturregelung im Ofen.
Ein wesentliches Merkmal des Muffelofens ist seine Fähigkeit, eine abgedichtete Umgebung zu schaffen und so den Kontakt zwischen Probe und Luft zu reduzieren. Dadurch eignet er sich besonders für Experimente, die sauerstoffarme oder sauerstofffreie Bedingungen erfordern. Unter Hochtemperaturbedingungen kann die Probe physikalische Veränderungen (wie Schmelzen oder Verdampfen) oder chemische Reaktionen (wie Oxidation, Reduktion oder Zersetzung) durchlaufen. Während dieser Prozesse regelt der Muffelofen die Temperatur präzise über sein Steuerungssystem und gewährleistet so die Kontrolle der Reaktionen und die Reproduzierbarkeit der Versuchsergebnisse.
3. Hauptanwendungen und Reaktionsprozesse des Muffelofens
3.1 Wärmebehandlung von Metallen
In der Metallurgie werden Muffelöfen häufig für die Wärmebehandlung von Metallen eingesetzt. Die Wärmebehandlung ist eine wichtige Methode zur Veränderung der physikalischen und mechanischen Eigenschaften von Metallen, einschließlich Glühen, Abschrecken und Anlassen. Die Muffelofen bietet eine stabile und kontrollierbare Hochtemperaturumgebung, um die Wärmebehandlungsanforderungen verschiedener Metallmaterialien zu erfüllen.
- Glühprozess: Das Metall wird im Muffelofen auf eine bestimmte Temperatur erhitzt, für eine bestimmte Zeit gehalten und anschließend langsam abgekühlt. Dieser Prozess trägt dazu bei, innere Spannungen im Material abzubauen und dessen Duktilität und Zähigkeit zu verbessern.
- Abschreckprozess: Das Metall wird zunächst im Muffelofen auf eine kritische Temperatur erhitzt und dann schnell in ein Kühlmittel (wie Wasser oder Öl) getaucht, um das Metall schnell abzukühlen und so seine Härte und Festigkeit zu verbessern.
- Temperierprozess: Nach dem Abschrecken wird das Metall einer Wärmebehandlung unterzogen, normalerweise bei einer Temperatur, die niedriger ist als die Abschrecktemperatur, um seine Zähigkeit zu verbessern und die Sprödigkeit zu verringern.
Während dieser Wärmebehandlungsprozesse sorgt der Muffelofen für eine stabile Hochtemperaturumgebung und minimiert gleichzeitig die Belastung des Metalls mit Luftsauerstoff, wodurch eine Oxidation verhindert wird.
3.2 Keramisches Sintern
Beim Sinterprozess von Keramikmaterialien werden Keramikpulver auf hohe Temperaturen erhitzt, um die Bindung zwischen den Partikeln zu fördern und eine feste Struktur zu bilden. Die hohe Temperatur im Muffelofen ist entscheidend für das Sintern von Keramik. Während dieses Prozesses diffundieren und rekristallisieren die Pulverpartikel mit steigender Temperatur und bilden schließlich ein dichtes Keramikmaterial.
Die Temperaturkontrolle ist während des Sinterprozesses äußerst wichtig. Bei zu hoher Temperatur kann das Keramikmaterial schmelzen, bei zu niedriger Temperatur ist das Sintern unvollständig. Daher spielt die präzise Temperaturregelung des Muffelofens beim Keramiksintern eine entscheidende Rolle.
3.3 Veraschung und Zersetzung in chemischen Experimenten
Der Muffelofen wird häufig in der chemischen Analytik für Veraschungs- und Zersetzungsprozesse eingesetzt, insbesondere in der anorganischen Chemie. Veraschung ist ein Verfahren zum Entfernen organischer Substanzen aus einer Probe. Durch Erhitzen der Probe im Muffelofen auf eine bestimmte Temperatur werden organische Stoffe in Gase zersetzt und freigesetzt, wobei der Ascherückstand zurückbleibt.
In einigen chemischen Experimenten Muffelofen wird auch zur Erleichterung von Zersetzungsreaktionen eingesetzt. Beispielsweise können bestimmte Mineralien und Metallverbindungen bei hohen Temperaturen im Muffelofen Reduktions-, Oxidations- oder Zersetzungsreaktionen durchlaufen. Bei diesen Prozessen sind eine präzise Temperaturkontrolle und die Aufrechterhaltung einer sauerstofffreien Umgebung entscheidend für den Erfolg der Reaktionen.
3.4 Umweltüberwachung und Analyse organischer Verbindungen
Der Muffelofen wird auch häufig in der Umweltüberwachung eingesetzt. Beispielsweise können organische Schadstoffe in Boden- und Wasserproben analysiert oder der Brennstoffaschegehalt bestimmt werden, indem die Proben im Muffelofen erhitzt und die Produkte nach der Veraschung analysiert werden. Bei solchen Experimenten trägt die Hochtemperaturumgebung des Muffelofens dazu bei, organische Bestandteile aus den Proben zu entfernen und so die Genauigkeit und Wiederholbarkeit der Versuchsdaten zu gewährleisten.
4. Detaillierte Analyse der Reaktionsprozesse
Die spezifischen Reaktionsmechanismen im Muffelofen variieren je nach Versuchszweck und Probenart. Beispielsweise erfährt das Metall bei der Wärmebehandlung während des Erhitzens verschiedene physikalische und chemische Veränderungen. Beim Glühen wird die Gitterstruktur des Metalls neu geordnet und intermolekulare Spannungen werden abgebaut. Beim Abschrecken verändert sich durch schnelles Abkühlen die Kristallstruktur des Metalls drastisch: Es bildet sich eine dichtere Gitterstruktur, wodurch die Härte steigt.
Beim Sintern von Keramik erhöht die Temperaturerhöhung die atomare Aktivität an der Partikeloberfläche und ermöglicht so deren Bindung durch Diffusion. Oxidations- und Reduktionsreaktionen, die bei chemischen Analysen im Muffelofen häufig vorkommen, beinhalten typischerweise die Freisetzung oder Aufnahme von Wärme. Daher ist bei der Durchführung dieser Reaktionen eine präzise Kontrolle der Heizrate und der Reaktionsatmosphäre erforderlich.
5. Fazit
Als Hochtemperatur-Experimentiergerät spielt der Muffelofen eine wichtige Rolle bei der Bereitstellung einer sauerstofffreien oder sauerstoffarmen Umgebung, was zu seiner weit verbreiteten Anwendung in verschiedenen Bereichen geführt hat. Ob bei der Metallwärmebehandlung, dem Keramiksintern oder der chemischen Probenanalyse – der Muffelofen gewährleistet stabile Versuchsbedingungen, kontrolliert den Prozess und gewährleistet die Reproduzierbarkeit der Ergebnisse. Eine detaillierte Analyse der Reaktionsprozesse im Muffelofen verdeutlicht seine Bedeutung in den Bereichen Materialwissenschaft, Chemieingenieurwesen und anderen Bereichen. Mit dem technologischen Fortschritt dürften sich Anwendungsbereich und Präzision des Muffelofens zukünftig weiter ausweiten.
Kemi Muffelofen
Kemi BFC-1200-18L Hochtemperatur-Muffelofen ist für effizientes Heizen mit einem dreiseitigen Heizsystem konzipiert, das eine schnelle und gleichmäßige Temperaturverteilung gewährleistet. Mit einer Maximaltemperatur von 1200 °C bietet er eine präzise Temperaturregelung (±1 °C) mittels PID-Regler und eine digitale Anzeige für verbesserte Genauigkeit und reduzierte manuelle Fehler. Der Ofen hat ein Fassungsvermögen von 18 Litern und eine Leistung von 5 kW. Er verfügt über moderne Isoliermaterialien und einen doppelschichtigen Luftkühlungsmechanismus, der die Außentemperatur unter 60 °C hält. Der Ofen ist energieeffizient und verbraucht im Vergleich zu ähnlichen Modellen nur ein Viertel des Stroms. Sicherheitsfunktionen wie ein Not-Aus-Schalter, ein Übertemperaturalarm und ein Alarm bei unterbrochener Verbindung sorgen für mehr Sicherheit und Langlebigkeit.
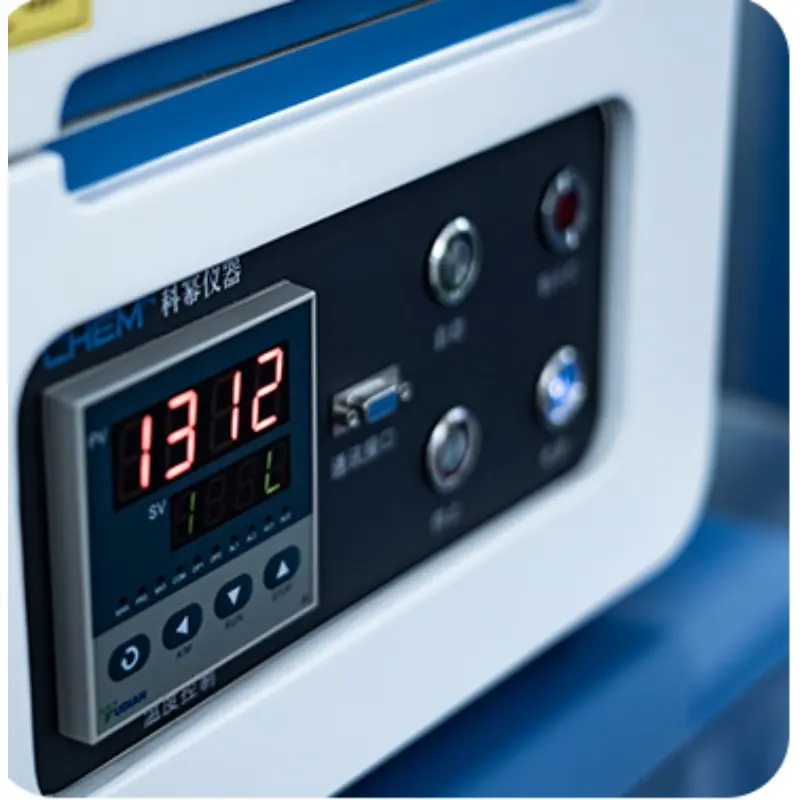
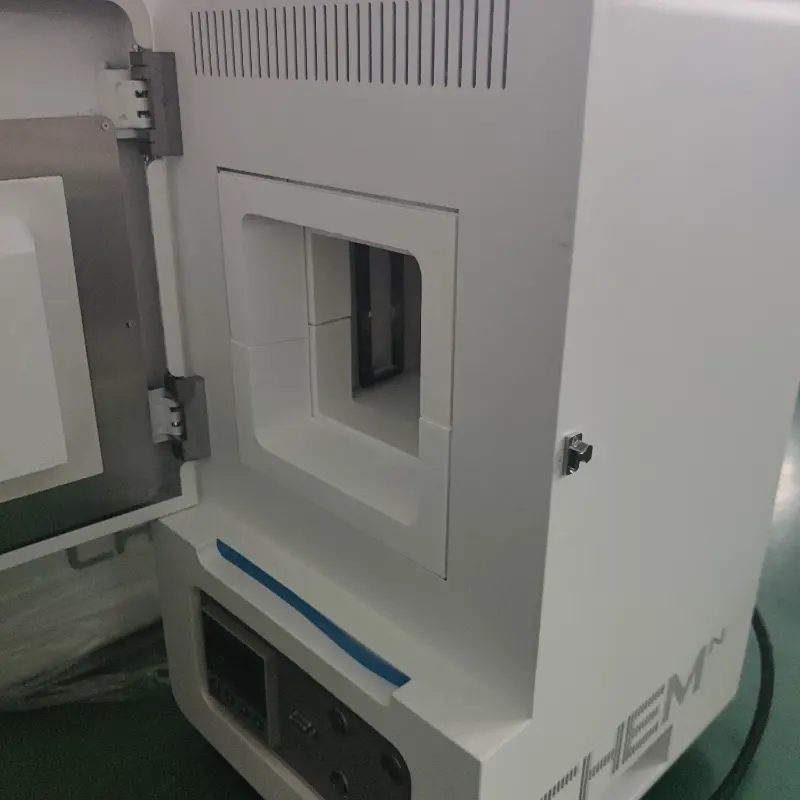
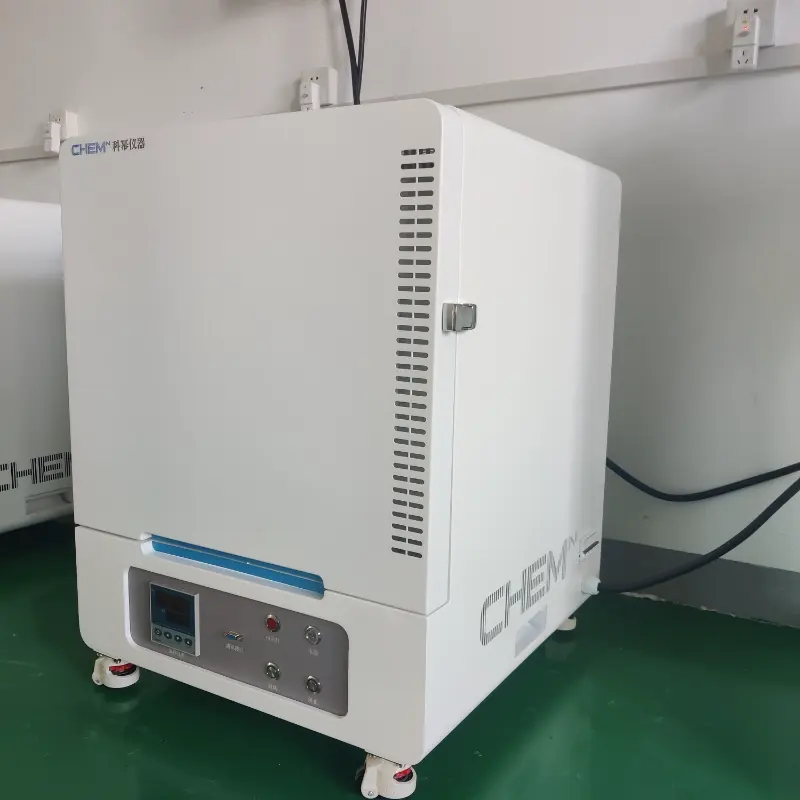